INDUSTRY SCENARIO – DETERGENT PRODUCTION
AI-assisted on-the-job training for production line operators
Objectives and Background
Increase efficiency of production and reduce change over time
Capturing the best practices and transferring them between manufacturing lines
Tacit line-manager knowledge capturing, formalising, and transfer to co-workers
The Diversey liquid production use case focusses on the implementation of COALA Digital Intelligent Assistant (DIA) to support production line operatos towards optimum configuration of the production line for each product.
Setup and change-over of production lines are complex and time consuming activities that require trained workers ccapably of (re)configure machnies, align production speeds, and adjust machine settings within a given amount of time. Both production line setup and change-over are non-value added operations and should be minimised as much as possible.
Change-over time or downtime currently consumes 40-45% of the total production time on average. Diversey aims to tackle the challenge of agile manufacturing by continuously optimizing the process of production line reconfiguration and by training and re-training of production line managers with the help of a digital assistant.
Expected Impacts
Business Scenario #1:
Faster line re-configuration and on-job training for line managers
AS-IS situation
• High change-over time and unscheduled downtime
• Reconfiguration time variation
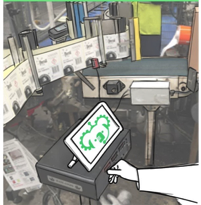
TO-BE situation
• Production line operators to request advices, explanations, and other information during the change-over
• Guide workers towards optimum configuration of the production line for each product and formulation
• Reduce the change over time, time pressure caused by downtime, and lessen the cognitive workload of workers in solving unpredictable
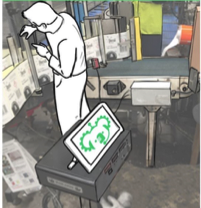
Business Scenario #2:
Training of production line managers
AS-IS situation
• Training in for production workers takes 2-3 months.
• Experience and understanding the proper settings takes longer.
•Best practice and to run the line the most effective way takes years.
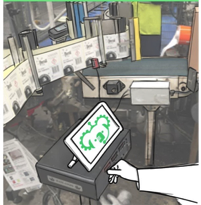
TO-BE situation
• Capture, formalize and contextualize tacit knowledge of product line managers about setup, reconfiguration, running, and maintenance of production lines
• Transfer tacit knowledge of product line managers to inexperienced co-workers
• Standardize tacit knowledge of multiple experienced operators of the same production line
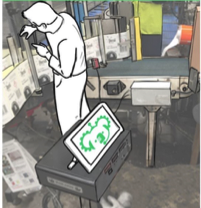